27.04.2022
Группа 406
Предмет: Слесарное дело и технические измерения
Тема урока: Приемы притирки поверхностей
Цель урока :изучить данную тему, составить конспект урока
Ручная притирка состоит из нескольких последовательно выполняемых рабочих приемов:
А) подготовка притира и обрабатываемой поверхности;
Б) накладывание притира на поверхность детали (или детали на притир) и перемещение их относительно друг друга с определенным давлением и скоростью;
В) контроль формы, размеров и шероховатости поверхности.
Эти рабочие приемы повторяются до полной обработки поверхности детали.
Подготовка к притирке. Начинать следует с проверки точности формы притира. Рабочая поверхность притира перед началом работы должна быть точно отшлифована и доведена, а также тщательно очищена от отходов абразива. Притир промывают в бензине или керосине и насухо протирают ветошью.
При притирке деталей твердыми абразивами следует производить принудительное шаржирование притира, которое заключается во вдавливании в поверхность притира зерен абразивного материала. Это необходимо для укрепления зерен в мягкой поверхности притира. В противном случае зерна абразивного материала до их укрепления в процессе притирки будут перекатываться между притиром и деталью и портить поверхность детали.
При притирке мягкими абразивами процесс шаржирования заключается в свободном нанесений равномерным слоем на поверхность притира или де-
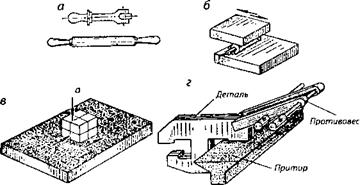
Рис. 137. Приемы притирки и подготовки к ней: а — оправки (шарниры) для шаржирования; б — схема шаржирования круглого притира абразивным порошком; в — направление приложения усилий при доводке; г — уравновешивание притираемых скоб |
Тали определенного слоя пасты в полужидком состоянии.
Покрытие притира абразивным порошком может быть прямым и косвенным. При прямом покрытии притира абразивным порошком последний вдавливается в притир до начала работы. Этот прием выполняется так: поверхность притира, покрытого тонким слоем смазки, посыпают ровным слоем абразивного порошка, затем при помощи стального закаленного бруска, ролика или цилиндрического валика (рис. 137, а) вдавливают порошок в притир. Круглые притиры катают между двумя твердыми стальными плитами до тех пор (рис. 137, 6), пока абразив не вдавится в поверхность притира.
При косвенном покрытии притира абразивным порошком покрывают не притир, а притираемую поверхность детали, и уже в процессе притирки абразивный порошок вдавливается в притир, изготовленный из более мягкого материала, чем притираемая деталь. Шаржированный таким способом притир будет иметь поверхность, состоящую из большого количества мелких твердых с режущими ребрами зерен.
При притирке и доводке следует учитывать, что чем выше требование к чистоте поверхности, тем тоньше должен быть слой абразива и смазки, наносимых на притир.
Приемы выполнения притирки. Подготовленную для притирки деталь аккуратно укладывают на шаржированный притир или, наоборот, притир — на поверхность детали и круговыми в сочетании с прямыми движениями перемещают ее по всей поверхности притира. Нажим на деталь должен быть равномерным и не сильным, а движения рук — плавными. Для предотвращения завалов и перекосов вертикальное усилие О нужно прилагать в точке, расположенной ближе к работающему (рис. 137, в), а горизонтальное усилие Р — в наиболее низкой точке детали, расположенной ближе к притиру; при этом деталь будет уравновешена.
После 10—11 таких движений абразивный порошок притупляется и его удаляют. Затем чистой ветошью протирают деталь и прекращают притирку после того, как поверхность детали примет матовый или зеркальный вид.
В процессе притирки постепенно переходят от крупнозернистых к мелкозернистым порошкам или пастам. Если в этом случае пользуются одним и тем же притиром, следует при каждой смене абразива тщательно промывать притир и протирать насухо с целью удаления остатков абразива от предыдущей притирки. Если этого не сделать, то оставшиеся на притире более крупные зерна абразива будут портить поверхность детали.
Притирку плоских поверхностей обычно выполняют в два приема: предварительную притирку — на вращающихся притирах с канавками, а окончательную — на неподвижных притирах с гладкой поверхностью. На плитах притирают детали, требующие высокой точности, например лекальные линейки, шаблоны, плитки, калибры.
Притирка наружных цилиндрических поверхностей, как правило, производится на токарных или специально для этой цели приспособленных сверлильных станках. Притирами при этом служат разрезные (регулируемые) чугунные или медные втулки и кольца (рис. 138, а, в). В ряде случаев пользуются притирами, имеющими форму плоского напильника.
Притирка цилиндрических отверстий выполняется с помощью чугунных или медных стержней и втулок. Простейший притир представляет собой разрезную втулку 1 (рис. 138, б), надетую на оправку 2 с конусной посадочной частью. Перемещая втулку-при - тир вдоль оправки, можно изменять наружный диаметр притира в соответствии с действительным размером притираемого отверстия. Установив таким образом нужный размер, втулку-притир покрывают абразивным порошком с маслом или пастой ГОИ с керосином и закрепляют в патроне станка. Затем включают станок и, надев деталь на притир, сообщают ей медленное возвартно-поступательное движение. Во время притирки деталь удерживают в руках или в специальном держателе.
Притирка конических поверхностей производится специальными притирами — пробками, имеющими канавки для удержания притирочного вещества (рис. 136, е, ж), или притирами-кольцами. Нанеся на притир ровным слоем смазку с разведенным в ней абразивным порошком, вводят притир в отверстие

------------- -йй-Г-1----------- -------------------- —- |
Рис. 138. Притирка поверхностей: а, б, в — цилиндрических; г — конических
Или накладывают на обрабатываемый конус и вручную воротком или коловоротом сообщают ему вращение вокруг оси. Можно вести обработку также на токарном или сверлильном станке. После 10—11 движений снимают притир, насухо вытирают его и притираемую поверхность; операцию притирки повторяют до тех пор, пока вся обрабатываемая поверхность не станет матовой или глянцевой.
Детали кранов и клапанов притирают по взаимно сопрягающимся поверхностям без применения специальных притиров. Чтобы, например, притереть пробку крана к коническому гнезду, поступают следующим образом. На пробку крана наносят слой средней пасты, вставляют ее в гнездо и поворачивают то в одну, то в другую сторону (рис. 138, г), следя за тем, чтобы притирка происходила по всей поверхности пробки и гнезда крана. Для проверки плотности притирки пробку и гнездо крана тщательно вытирают, затем на пробке проводят вдоль притираемой поверхности мелом или цветным карандашом черту и, вставив пробку в гнездо, поворачивают ее вокруг оси.
Если притирка сделана хорошо, то черта сотрется равномерно по всей длине пробки крана.
Приемы проверки обработанных деталей. Проверку и измерение обработанных притиркой плоскостей производят лекальной линейкой на просвет. При притирке и доводке, выполненной с точностью 0,001 мм, лекальная линейка должна ложиться на обработанную плоскость без всякого просвета.
Параллельность проверяют штангенциркулем, микрометром, индикатором, миниметром и оптиметром с точностью от 0,05 до 0,00025 мм в зависимости от применяемого инструмента. Углы проверяют угольником, угломером, шаблоном, плиточно-угло - выми эталонами и синусной линейкой. Проверку конических отверстий обычно производят на краску по точно изготовленным и проверенным калибрам-пробкам. Профиль проверяют при помощи шаблонов, лекал и щупов.