31.01.2023
Группа 303
Предмет: Технология газовой сварки
Тема урока: Оборудование для сварки цветных металлов
Цель урока: изучить данную тему, составить конспект урока
Электроды для сварки цветных металлов
Для каждого цветного металла, который поддается дуговой сварке, разработаны специальные электроды.
Электроды для сварки алюминия. Для изготовления электродов для сварки алюминия технической чистоты, силумина и сплавов АМц выбирают марку проволоки, состав которой наиболее близок к основному металлу. Основу покрытий электродов для сварки алюминия и его сплавов составляют легкоплавкие хлористые и фтористые соли щелочных и щелочноземельных металлов а также криолит (Na3AlF6).
Технический алюминий сваривают электродами марок ОЗА-1, ЭА-1, ЭА-11Ф1, МАТИ-2.
Сплавы типа АМц сваривают электродами марки МВТУ.
Сплавы типа АМrсваривают электродами марки 48-АЭ-1.
Сплавы типа АМц и АМrсваривают электродами марки ВАМИ, А1.
Сплавы типа АМц и силумин сваривают электродами марки А1, А1Ф.
Электроды для сварки меди изготавливаются из тянутой проволоки или круглых тянутых или прессованных прутков. К числу марок электродов для сварки меди и ее сплавов относятся следующие:
«Комсомолец», ММЗ-1, ММЗ-2, АНЦ-1, АНЦ-2, АНЦ/ОЗМ-2, АНЦ/ОЗМ-3 и АНЦ/ОЗМ-4.
Никель и его сплавы сваривают электродами марок Н-10, Н-30К, Н-37К, 48-Нк-1 и др.
Тема 1.2 Основы способа ручной дуговой сварки покрытым электродом. Схема процесса. Защита сварочной ванны. Технологические особенности сварки. Техника сварки. Сварочные материалы. Режимы сварки. Область целесообразного применения. Оборудование поста ручной дуговой сварки.
5 Сущность и техника ручной дуговой сварки металлическими электродами с покрытием
Сущность способа. К электроду и свариваемому изделию для образования и поддержания сварочной дуги от источников сварочного тока подводится постоянный и переменный ток (рисунок 24). Дуга расплавляет металлический стержень электрода, его покрытие и основной металл. Расплавляющийся металлический стержень электрода в виде отдельных капель, покрытых шлаком, переходит в сварочную ванну. В сварочной ванне электродный металл смешивается с расплавленным металлом изделия (основным металлом), а расплавленный шлак всплывает на поверхность.

1-металлический стержень; 2-покрытие электрода; 3-газовая атмосфера дуги; 4-сварочная ванна; 5- затвердевший шлак; 6-акристаллизовавшийся металл шва; 7-основной металл (изделие); 8-капли расплавленного электродного металла; 9-глубина проплавления
Рисунок 24 - Ручная дуговая сварка металлическим электродом с
покрытием (стрелкой указано направление сварки)
Глубина, на которую расплавляется основной металл, называется глубиной проплавления. Она зависит от режима сварки (силы сварочного тока и диаметра электрода), пространственного положения сварки, скорости перемещения дуги по поверхности изделия, от конструкции сварного соединения, формы и размеров разделки свариваемых кромок и т. п. Размеры сварочной ванны зависят от режима сварки и обычно находятся в пределах: глубина до 7 мм( ширина 8—15 мм, длина 10—30 мм. Доли участия основного металла в формировании металла шва обычно составляет 15-35%.
Расстояние от активного пятна на расплавленной поверхности электрода до другого активного пятна дуги на поверхности сварочной ванны называется длиной дуги. Расплавляющееся покрытие электрода образует вокруг дуги и над поверхностью сварочной ванны газовую атмосферу, которая, оттесняя воздух из зоны сварки, препятствует взаимодействиям его с расплавленным металлом. В газовой атмосфере присутствуют также пары основного и электродного металлов и легирующих элементов. Шлак, покрывая капли электродного металла и поверхность расплавленного металла сварочной ванны, способствует предохранению их от контакта с воздухом и участвует в металлургических взаимодействиях с расплавленным металлом.
Кристаллизации металла сварочной ванны по мере удаления дуги приводит к образованию шва, соединяющего свариваемые детали. При случайных обрывах дуги или при смене электродов кристаллизация металла сварочной ванны приводит к образованию сварочного кратера (углублению в шве, по форме напоминающему наружную поверхность сварочной ванны). Затвердевающий шлак образует на поверхности шва шлаковую корку.
Ввиду того что от токоподвода в электрододержателе сварочный ток протекает по металлическому стержню электрода, стержень разогревается. Этот разогрев тем больше, чем дольше протекание по стержню сварочного тока и чем больше величина последнего Перед началом сварки металлический стержень имеет температуру окружающего воздуха, а к концу расплавления электрода температура повышается до 500 - 6000С (при содержании в покрытии органических веществ — не выше 2500С). Это приводит к тому, что скорость расплавления электрода (количество расплавленного электродного металла) в начале и конце различна. Изменяется и глубина проплавления основного металла ввиду изменения условий теплопередачи от дуги к основному металлу через прослойку жидкого металла в сварочной ванне. В результате изменяется соотношение долей электродного и основного металлов, участвующих в образовании металла шва, а значит, и состав и свойства металла шва, выполненного одним электродом. Это — один из недостатков ручной дуговой сварки покрытыми электродами.
Зажигание и поддержание дуги. Перед зажиганием (возбуждением) дуги следует установить необходимую силу сварочного тока, которая зависит от марки электрода, пространственного положения сварки, типа сварного соединения и др. Зажигать дугу можно двумя способами. При одном способе электрод приближают вертикально к поверхности изделия до касания металла и быстро отводят вверх на необходимую длину дуги. При другом - электродом вскользь «чиркают» по поверхности металла. Применение того или иного способа зажигания дуги зависит от условия сварки и от навыка сварщика.
Техника ручной дуговой сварки. Под техникой сварки обычно понимают приемы манипулирования электродом или горелкой, выбор режимов сварки, приспособлений и способы их применения дли получения качественного шва и т. п. Качество швов зависит не только от техники сварки, по и от других факторов, таких как состав и качество применяемых сварочных материалов, состояние свариваемой поверхности, качество подготовки и сборки кромок под сварку и т. д.
В зависимости от формы и размеров изделия швы можно сваривать в различных пространственных положениях (рисунок 12).
Техника манипулирования электродом. Во время сварки сварщик сообщает концу электрода движение в трех направлениях.
Первое движение — поступательное по направлению оси электрода, для поддержания необходимой длины дуги LД, которая должна быть
LД= (0,5 ÷1,1)dэ.
Длина дуги оказывает большое влияние на качество сварного шва и его форму. Увеличение длины дуги снижает качество наплавленного металла шва ввиду его интенсивного окисления и азотирования, увеличивает потери металла на угар и разбрызгивание, уменьшает глубину проплавления основного металла. Также ухудшается внешний вид шва.
Второе движение — вдоль оси валика для образования сварного шва. Скорость движения электрода зависит от величины тока, диаметра электрода, типа и пространственного положения, в котором выполняется шов. Правильно выбранная скорость перемещения электрода вдоль оси шва обеспечивает требуемую форму и качество сварного шва. При большей скорости перемещения электрода основной металл не успевает проплавляться, вследствие чего образуется непровар. Недостаточная скорость перемещения электрода приводит к перегреву и прожогу (сквозное проплавление) металла, а также снижает качество и производительность сварки. Правильно выбранная скорость продольного движения электрода вдоль оси шва позволяет получить его ширину на 2—3 мм больше, чем диаметр электрода.
Сварной шов, образованный в результате первого и второго движения электрода, называют ниточным. Его применяют при сварке металла небольшой толщины, при наплавочных работах и подварке подрезов.
Третье движение — колебание концом электрода поперек шва для образования уширенного валика, который применяют чаще, чем ниточный. Для образования уширенного валика электроду сообщают поперечные колебательные движения чаще всего с постоянной частотой и амплитудой, совмещенные с поступательным движением электрода вдоль оси подготовленного под сварку соединения и оси электрода. Поперечные колебательные движения электрода разнообразны и определяются формой, размерами, положениями шва в пространстве, в котором выполняется сварка, и навыком сварщика. На рисунке 3 показаны поперечные колебания, описываемые концом электрода. В процессе колебания электрода середину пути проходят быстро, задерживая электрод по краям. Такое изменение скорости колебания электрода обеспечивает лучший провар по краям. Ширина валика не должна быть более 2 — 3 диаметров электрода, что соответствует ГОСТ и технологии сварки. При выполнении более широких валиков в результате охлаждения шлака возможно образование дефектов в сварном шве.
Обычно сварку выполняют вертикально расположенным электродом или при его наклоне относительно шва, углом вперед или назад (рисунок 25). При сварке углом назад улучшаются условия оттеснения из-под дуги жидкого металла, толщина прослойки которого уменьшается. При этом улучшаются условия теплопередачи от дуги к основному металлу и растет глубина его проплавления.
То же наблюдается при сварке шва на подъем на наклонной или вертикальной плоскости. При сварке углом вперед или на спуск расплавленный металл сварочной ванны, подтекая под дугу, ухудшает теплопередачу от нее к основному металлу — глубина проплавления уменьшается, а ширина шва возрастает (сечения швов на рисунке 26).
При прочих равных условиях количество расплавляемого электродного металла, приходящегося на единицу длины шва, остается постоянным, но распределяется на большую ширину шва и поэтому высота его усиления уменьшается. При наплавке или сварке тонколистового металла (толщина до 3 мм) для уменьшения глубины провара и предупреждения прожогов рекомендуется сварку выполнять на спуск (наклон до 15°) или углом вперед без поперечных колебаний электрода. Для сборки изделия под сварку (обеспечения заданного зазора в стыке, положения изделий и др.) можно применять специальные приспособления или короткие швы — прихватки. Длина прихваток обычно составляет 20— 120 мм (больше при более толстом металле) и расстояние между ними 200—1200 мм (меньше при большей толщине металла для увеличения жесткости). Сечение прихваток не должно превышать 1/3 сечения швов. При сварке прихватки необходимо полностью переплавлять.
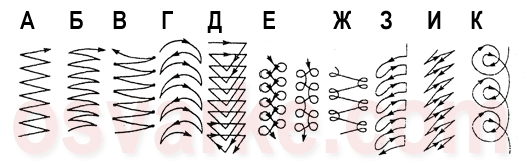
Рисунок 25 – Основные виды траекторий движений конца электрода при слабом прогреве (А, Б, В, Г), усиленном прогреве середины (Д), свариваемых кромок (Е-Ж) , усиленном прогреве одной кромки (З, И), прогреве корня шва (К).
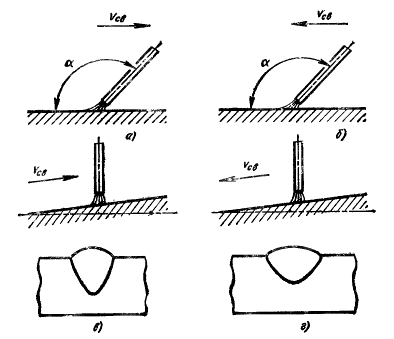
а) углом назад, б) углом вперед, в) на подъем, г) на спуск
Рисунок 26 – Способы выполнения сварки
При прочих равных условиях количество расплавляемого электродного металла, приходящегося на единицу длины шва, остается постоянным, но распределяется на большую ширину шва и поэтому высота его усиления уменьшается. При наплавке или сварке тонколистового металла (толщина до 3 мм) для уменьшения глубины провара и предупреждения прожогов рекомендуется сварку выполнять на спуск (наклон до 15°) или углом вперед без поперечных колебаний электрода. Для сборки изделия под сварку (обеспечения заданного зазора в стыке, положения изделий и др.) можно применять специальные приспособления или короткие швы — прихватки. Длина прихваток обычно составляет 20— 120 мм (больше при более толстом металле) и расстояние между ними 200—1200 мм (меньше при большей толщине металла для увеличения жесткости). Сечение прихваток не должно превышать 1/3 сечения швов. При сварке прихватки необходимо полностью переплавлять.
Техника сварки в нижнем положении. Это пространственное положение позволяет получать сварные швы наиболее высокого качества, так как облегчает условия выделения неметаллических включений, газов из расплавленного металла сварочной ванны. При этом также наиболее благоприятны условия формирования металла шва, так как расплавленный металл сварочной ванны от вытекания удерживается нерасплавившейся частью кромок.
Стыковые швы сваривают без скоса кромок или с V-, Х- и U-образным скосом. Положение электрода относительно поверхности изделия и готового шва показано на рисунке 27. Стыковые швы без скоса кромок в зависимости от толщины сваривают с одной или двух сторон. При этом концом электрода совершают поперечные колебания (см. рисунок 3) с амплитудой, определяемой требуемой шириной шва. Следует тщательно следить за равномерным расплавлением обеих свариваемых кромок по всей их толщине и особенно стыка между ними в нижней части (корня шва).
Однопроходную сварку с V-образным скосом кромок обычно выполняют с поперечными колебаниями электрода на всю ширину разделки для ее заполнения так, чтобы дуга выходила со скоса кромок на необработанную поверхность металла. Однако в этом случае очень трудно обеспечить равномерный провар корня шва по всей его длине, особенно при изменении величины притупления кромок и зазора между ними.
Однопроходную сварку с V-образным скосом кромок обычно выполняют с поперечными колебаниями электрода на всю ширину разделки для ее заполнения так, чтобы дуга выходила со скоса кромок на необработанную поверхность металла. Однако в этом случае очень трудно обеспечить равномерный провар корня шва по всей его длине, особенно при изменении величины притупления кромок и зазора между ними.
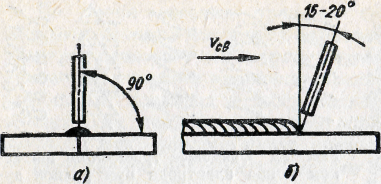
а) поперек оси шва, б) сбоку
Рисунок 27 - Положение электрода при сварке в нижнем
положении
При сварке шва с V-образным скосом кромок за несколько проходов обеспечить хороший провар первого слоя в корне разделки гораздо легче. Для этого обычно применяют электроды диаметром 3—4 мм и сварку ведут без поперечных колебаний. Последующие слои выполняют в зависимости от толщины металла электродом большего диаметра с поперечными колебаниями. Для обеспечения хорошего провара между слоями предыдущие швы и кромки следует тщательно очищать от шлака и брызг металла. Заполнять разделку кромок можно швами с шириной на всю разделку или отдельными валиками (рисунок 28). В многопроходных швах последний валик (11 на рисунке 5, в) для улучшения внешнего вида иногда можно выполнять на всю ширину разделки (декоративный слой).
Сварку швов с Х- или U-образным скосом кромок выполняют в общем так же, как и с V-образным скосом. Однако для уменьшения остаточных деформаций и напряжений, если это возможно, сварку ведут, накладывая каждый валик или слой попеременно с каждой стороны. Швы с Х- или U-образным скосом кромок по сравнению с V-образным имеют преимущества, так как в первом случае в 1,6—1,7 раза уменьшается объем наплавленного металла (повышается производительность сварки). Кроме того, уменьшаются угловые деформации, а возможный непровар корня шва образуется в нейтральном по отношению к изгибающему моменту сечении. Недостаток U-образного скоса кромок — повышенная трудоемкость его получения.
Сварку стыковых швов можно выполнять различными способами (рисунок 29). При сварке на весу и выполнения корневого шва при многослойной сварке наиболее трудно обеспечить удержание расплавленного металла в сварочной ванне и формирование хорошего обратного валика по всей длине стыка.
Для предупреждения вытекания расплавленного металла из сварочной ванны применяют стальные, медные, керамические или асбестовые подкладки, устанавливаемые под корень шва; обходятся без сквозного проплавления с последующей подрубкой и подваркой корня шва с противоположной стороны; флюсовые, флюсо-медные и газовые подушки, устанавливаемые под корень шва; при стыковой сварке — соединения «в замок».
Подкладки позволяют увеличивать величину сварочного тока, способствуя сквозному проплавлению свариваемых кромок и обеспечивая при этом 100%-ный провар свариваемых деталей. Для предупреждения вытекания расплавленного металла из сварочной ванны подкладки должны плотно прилегать к свариваемым кромкам.
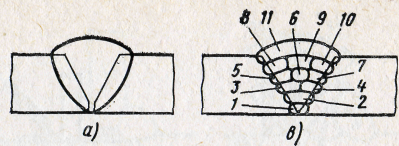
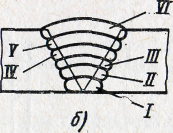
а) однопроходных, б) многослойных, в) многопроходных
1- V1 – слои, 1-11- проходы
Рисунок 28- Поперечные сечения стыковых швов

а) на весу, б) на медной съемной подкладке, в) на остающейся стальной подкладке, г) с предварительным подварочным швом, д) удаление непровара в корне шва для последующей подварки; 1- медная подкладка, 2- остающаяся подкладка, О - основной шов, П - подварочный шов.
Рисунок 29 - Схемы сварки
Иногда по заранее продуманной технологии не делают сквозного проплавления свариваемых кромок, а затем с обратной стороны делают канавку газовой или воздушной - дуговой строжкой или механическими методами (рисунок 6, д) накладывают подварочный шов, обеспечивая при этом 100%-ный провар свариваемых кромок в корне шва.Если с обратной стороны возможен подход к корню шва и допустимо усиление обратной стороны шва, целесообразна (рисунок 6, г) подварка корня швом небольшого сечения с последующей укладкой основного шва.
Расплавленный металл сварочной ванны в корне шва удерживают применением различных подушек. Флюсовые и флюсо-медные подушки применяют при сварке под флюсом. Газовую подушку используют при ручной дуговой сварке, ручной и автоматической аргонодуговой сварке с использованием в качестве поддувочного газа аргона, азота или углекислого газа. Сущность газовой подушки состоит в том, что под расплавленный металл сварочной ванны подается один из выше упомянутых газов с избыточным давлением 0,5 —2кПа.
Сварку угловых швов в нижнем положении можно выполнять двумя приемами. Сварка вертикальным электродом в лодочку (рисунок 30, а) обеспечивает наиболее благоприятные условия для провара корня шва и формирования его усиления. По существу этот прием напоминает сварку стыковых швов с V-образным скосом кромок, так как шов формируется между свариваемыми поверхностями. Однако при этом способе требуется тщательная сборка соединения под сварку с минимальным зазором в стыке для предупреждения вытекания в него расплавленного металла.
При сварке наклонным электродом (рисунок 30, б- г) трудно обеспечить провар шва по нижней плоскости (ввиду натекания на нее расплавленного металла) и предупредить подрез на вертикальной плоскости (ввиду стекания расплавленного металла). Поэтому таким способом обычно сваривают швы с катетом до 6—8 мм.
При сварке угловых швов наклонным электродом трудно также обеспечить глубокий провар в корне шва, поэтому в односторонних или двусторонних швах без скоса кромок может образоваться непровар (рисунок 31, а), который при нагружении шва послужит началом развития трещин. Для предупреждения этого в ответственных соединениях при толщине металла 4 мм и более необходим односторонний скос, а при толщине 12 мм и более - двусторонний скос кромок.
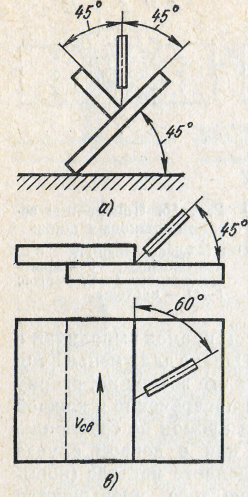
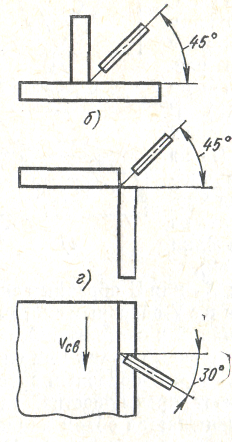
а) в лодочку; б) таврового соединения; в) внахлестку; г) углового
соединения
Рисунок 30 – Положение электрода и изделия при сварке
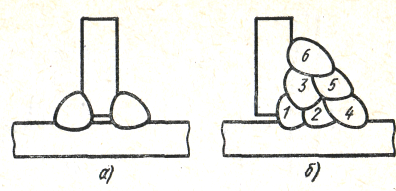
1 - 6 последовательность наложения швов
Рисунок 31 – Сварка угловых швов
При сварке наклонным электродом многопроходных швов первым выполняют шов на горизонтальной плоскости (рисунок 31, б). Формирование последующего валика происходит с частичным удержанием расплавленного металла сварочной ванны нижележащим валиком. При сварке угловых швов применяют поперечные колебания электрода. Особенно важен правильный выбор их траектории при сварке наклонным электродом с целью предупреждения возникновения указанных выше дефектов.
Техника сварки на горизонтальной и потолочной плоскостях. Сварка швов в положениях, отличающихся от нижнего, требует повышенной квалификации сварщика в связи с возможным под действием сил тяжести вытеканием расплавленного металла из сварочной ванны или падением капель электродного металла мимо сварочной ванны. Для предотвращения этого сварку следует вести по возможности наиболее короткой дугой, в большинстве случаев с поперечными колебаниями.
Расплавленный металл в сварочной ванне от вытекания удерживается в основном силой поверхностного натяжения. Поэтому необходимо уменьшать ее размер, для чего конец электрода периодически отводят в сторону от ванны, давая возможность ей частично закристаллизоваться. Ширину валиков также уменьшают до двух-трех диаметров электродов. Применяют пониженную на 10-20% силу тока и электроды уменьшенного диаметра (для вертикальных и горизонтальных швов не более 5 мм, для потолочных не более 4 мм).
Сварку вертикальных швов можно выполнять на подъем или на спуск (рисунок 32). При сварке на подъем (рисунок 32,а) нижележащий закристаллизовавшийся металл шва помогает удержать расплавленный металл сварочной ванны. При этом способе облегчается возможность провара корня шва и кромок, так как расплавленный металл стекает с них в сварочную ванну, улучшая условия теплопередачи от дуги к основному металлу. Однако внешний вид шва - грубочешуйчатый. При сварке на спуск (рисунок 32,б) получить качественный провар трудно: шлак и расплавленный металл подтекают под дугу и от дальнейшего стекания удерживаются только силами давления дуги и поверхностного натяжения. В некоторых случаях их оказывается недостаточно, и расплавленный металл вытекает из сварочной ванны.
Сварка горизонтальных стыковых швов (рисунок 33) более затруднена, чем вертикальных, из-за стекания расплавленного металла из сварочной ванны на нижнюю кромку. В результате возможно образование подреза по верхней кромке. При сварке металла повышенной толщины обычно делают скос только одной верхней кромки, нижняя помогает удерживать расплавленный металл в сварочной ванне. При сварке стыковых швов с разделкой последний декоративный слой выполняют придвижении дуги под углом 45о к оси шва (рисунок 33, б). Сварка горизонтальных угловых швов в нахлесточных соединениях не вызывает трудностей и по технике не отличается от сварки в нижнем положении.
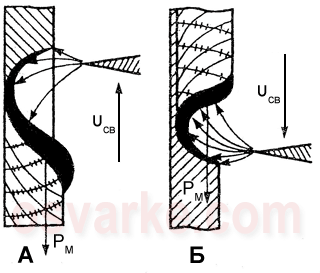
а) сварка на подъем, б) сварка на спуск
Рисунок 32 – Формирование ванны и шва при ручной дуговой сварке вертикальных швов
Сварка швов в потолочном положении (рисунок 34) наиболее сложна и ее по возможности следует избегать. Сварку выполняют периодическими короткими замыканиями конца электрода на сварочную ванну, во время которых металл сварочной ванны частично кристаллизуется, что уменьшает объем сварочной ванны. В то же время расплавленный электродный металл вносится в сварочную ванну. При удлинении дуги образуются подрезы. При сварке этих швов ухудшены условия выделения из расплавленного металла сварочной ванны шлаков и газов. Поэтому свойства металла шва несколько ниже, чем при сварке в других пространственных положениях.
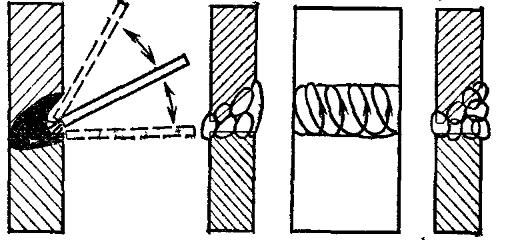
а) б) в)
а) за один проход , б) валиками с декоративным швом,
в) валиками без декоративного шва
Рисунок 33 – Ручная дуговая сварка горизонтальных швов
Техника сварки пробочных и прорезных соединений практически не отличается от рассмотренной выше техники сварки стыковых или угловых швов.
Порядок выполнения швов различной протяженности и толщины. Все сварные соединения по протяженности различают на три группы:
от 250 до 300 мм — короткие;
от 300 до 1000 мм — средней длины;
от 1000 мм и более — длинные.
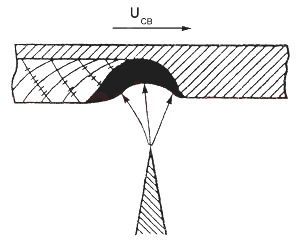
Рисунок 34 – Формирование ванны и шва при ручной дуговой сварке швов в потолочном положении
В зависимости от протяженности шва, толщины и марки металла, жесткости конструкции и т. д. применяют различные приемы последовательности сварки швов и заполнения разделки (рисунок 35). Сварку напроход обычно применяют при сварке коротких швов. Швы средней длины лучше сваривать от середины к концам или обратноступенчатым методом. При последнем способе весь шов разбивают на участки по 150-200 мм, которые должны быть кратны длине участка, наплавляемого одним электродом. Сварку швов в ответственных конструкциях большой толщины выполняют блоками, каскадом или горкой, что позволяет влиять на структуру металла шва и сварного соединения и его механические свойства.
При сварке горкой сначала в разделку кромок наплавляют первый слой небольшой длины 200-300 мм, затем второй слой, перекрывающий первый и имеющий в 2 раза большую длину. Третий слой перекрывает второй и длиннее его на 200-300 мм. Так наплавляют слои до тех пор, пока на небольшом участке над первым слоем разделка не будет заполнена. Затем от этой горки сварку ведут в разные стороны короткими швами тем же способом. Таким образом, зона сварки всё время находится в горячем состоянии, что позволяет предупредить появление трещин. Каскадный метод является разновидностью горки.

а) напроход, б) от середины к концам, в) обратноступенчато,
г) блоками, д) каскадом, е) горкой, А – направление заполнения
разделки. Стрелками указаны последовательность и направление
сварки в каждом слое (1-5)
Рисунок 35 – Сварка протяженных швов
Техника сварки кольцевых стыков труб. Сварка кольцевых стыков трубопроводов имеет некоторые специфические особенности. Обычно сваркой выполняют швы на трубах диаметром от десятков миллиметров до 1440 мм при толщине стенки до 16 мм и более. При толщине стенки труб из низкоуглеродистых и низколегированных сталей до 8-12 мм сварку можно выполнять в один слой. Однако многослойные швы имеют повышенные механические свойства, определяемые положительным влиянием термического цикла последующего шва на металл предыдущего шва, поэтому сварку труб преимущественно выполняют в два слоя и более. Рекомендуемое число слоев шва зависит от толщины стенки.
Наиболее распространена сварка труб с V- образной разделкой кромок с суммарным углом скоса кромок 50 – 60о. Перед сваркой стыки собирают в специальном приспособлении или на прихватках.
Стыки труб можно сваривать в поворотном, когда трубу можно вращать, или в неповоротном положении. Сварку швов первого типа выполняют обычно в нижнем положении без особых трудностей, хотя сложно проварить корень шва, так как его формирование ведется чаще всего на весу. Сварка неповоротного стыка требует высокой квалификации сварщика, так как весь шов выполняют в различных пространственных положениях. Можно сваривать двумя способами: каждое полукольцо сверху вниз или снизу вверх. Первый способ возможен при использовании электродов диаметром 4 мм, дающих мало шлака (с органическим покрытием), короткой дугой с опиранием образующегося на конце электрода козырька на кромки без поперечных колебаний электрода или с небольшими его колебаниями. При сварке снизу вверх процесс ведут со значительно меньшей скоростью с поперечными колебаниями электрода диаметром 3-5 мм.
При окончании сварки — обрыве дуги следует правильно заварить кратер. Кратер является зоной с наибольшим количеством вредных примесей ввиду повышенной скорости кристаллизации металла, поэтому в нем наиболее вероятно образованно трещин. По окончании сварки не следует обрывать дугу, резко отводя электрод от изделия. Необходимо прекратить все перемещения электрода и медленно удлинять дугу до обрыва; расплавляющийся при этом электродный металл заполнит кратер. При сварке низкоуглеродистой стали кратер иногда выводят в сторону от шва — на основной металл. При случайных обрывах дуги или при смене электродов дугу возбуждают на еще не расплавленном основном металле перед кратером и затем проплавляют металл в кратере.