15.05.2023
Группа 512
Предмет: Технология газовой сварки
Тема урока: Виды и схемы наплавок
Цель урока: изучить данную тему, составить конспект урока
Классификация способов наплавки
Способы наплавки, как и способы сварки, классифицируются по трем группам признаков: физическим, техническим и технологическим.
По физическим признакам (используемые источники нагрева) основные способы наплавки можно разделять на три класса: термический (наплавка дуговая, электрошлаковая, плазменная, электронно-лучевая, световая, индукционная, газовая, печная); термомеханический (наплавка контактная, прокаткой); механический (наплавка взрывом, трением).
Большинство из этих способов в свою очередь могут подразделяться по техническим (метод защиты металла в зоне наплавки, степень механизации наплавки, непрерывность процесса наплавки) и технологическим (по роду тока, по количеству электродов, по наличию внешнего воздействия и т. п.) признакам.
8.3. Термические способы наплавки
8.3.1. Ручная дуговая наплавка угольными и покрытыми электродами
Ручная дуговая наплавка угольными электродами (рис. 8.1, а) осуществляется путем расплавления слоя сыпучего зернистого наплавочного сплава.

Рис 8.1. Схемы основных способов дуговой наплавки: а – угольным (графитовым) электродом (1) расплавлением слоя сыпучего зернистого наплавляемого материала; б – ручной дуговой сваркой покрытым электродом (1) с легирующим покрытием (2); в – неплавящимся вольфрамовым электродом (1) в защитных инертных газах с присадочным прутком (2); г – плавящимся электродом (проволокой) (1) в среде защитных газов; д – электродной проволокой (1) под флюсом (7); е – плавящейся лентой (1) в защитных газах или под флюсом; во всех схемах: 3 – наплавляемая деталь; 4 – наплавленный слой
Ручная дуговая наплавка покрытыми электродами – наиболее универсальный способ для наплавки деталей различной формы, который может выполняться во всех пространственных положениях.
Легирование наплавленного металла производится через стержень электрода или через покрытие (рис.8.1, б). Электродное покрытие служит для защиты ванны жидкого металла от кислорода и азота воздуха, повышения технологичности процесса наплавки и введения легирующих элементов в состав наплавленного металла.
Для наплавки используют электроды диаметром 3 – 6 мм (при толщине наплавленного слоя менее 1,5 мм применяют электроды диаметром 3 мм, при большей – диаметром 4 – 6 мм). Для обеспечения минимального проплавления основного металла при достаточной устойчивости дуги плотность тока должна составлять 11 – 12 А/мм2.
Основные достоинства способа: универсальность и гибкость при выполнении разнообразных наплавочных работ; простота и доступность оборудования и технологии; возможность получения наплавленного металла практически любой системы легирования.
Основные недостатки способа: низкая производительность; тяжелые условия труда; нестабильность качества наплавленного слоя; большое проплавление основного металла.
8.3.2. Полуавтоматическая и автоматическая дуговая наплавка
Для наплавки применяются все основные способы механизированной дуговой сварки – под флюсом, в среде защитных газов и самозащитными проволоками и лентами.
При наплавке под флюсом (проволокой, лентой и др.) (рис.8.1, д, е) дуга скрыта под слоем гранулированного флюса, предварительно насыпанного на поверхность основного металла. Для наплавки под флюсом применяют электроды в виде одной или нескольких проволок диаметром 1 – 6 мм или электродной ленты толщиной 0,4 – 1,0 мм и шириной 20 – 100 мм. Расплавленный шлак надежно изолирует жидкий металл от газов воздуха, способствует сохранению теплоты дуги. После затвердевания металла образуется наплавленный валик, покрытый шлаковой коркой и нерасплавленным флюсом. Остывшую шлаковую корку удаляют. С помощью наплавки под флюсом можно наносить слой металла почти любого химического состава толщиной от 2 мм и более. Данный процесс применяют при наплавке цилиндрических поверхностей, а также всевозможных плоских деталей и изделий криволинейной формы (лопастей гидротурбин).
Процесс наплавки под флюсом отличается большой универсальностью, широкими возможностями легирования металла наплавленного слоя и повышенной производительностью труда.
Широкое распространение получила электродуговая наплавка лентой. Дуга на торце ленты (рис. 8.1, е) циклически перемещается от одной кромки к другой в зависимости от тока и ширины ленты со скоростью 1 – 4 м/с. Вследствие перемещения дуги получается рассеянное тепловложение в основной металл, что снижает глубину проплавления основного металла и долю его в наплавленном до 10 – 15 %.
На рис.8.2 приведены некоторые примеры, характеризующие пути повышения производительности труда и качества при наплавке под флюсом. Наибольшее распространение получили способы многоэлектродной и многодуговой наплавки.
Суть способа многоэлектродной электродуговой наплавки под флюсом заключается в том, что дуга автоматически возникает на торце то одного, то другого электрода, расположенных на определенном расстоянии друг от друга и имеющих один общий токоподвод. Дуга, перемещаясь с одного электрода на другой, приводит к попеременному плавлению электродов, чем обеспечивается малая глубина проплавления при высокой производительности процесса.
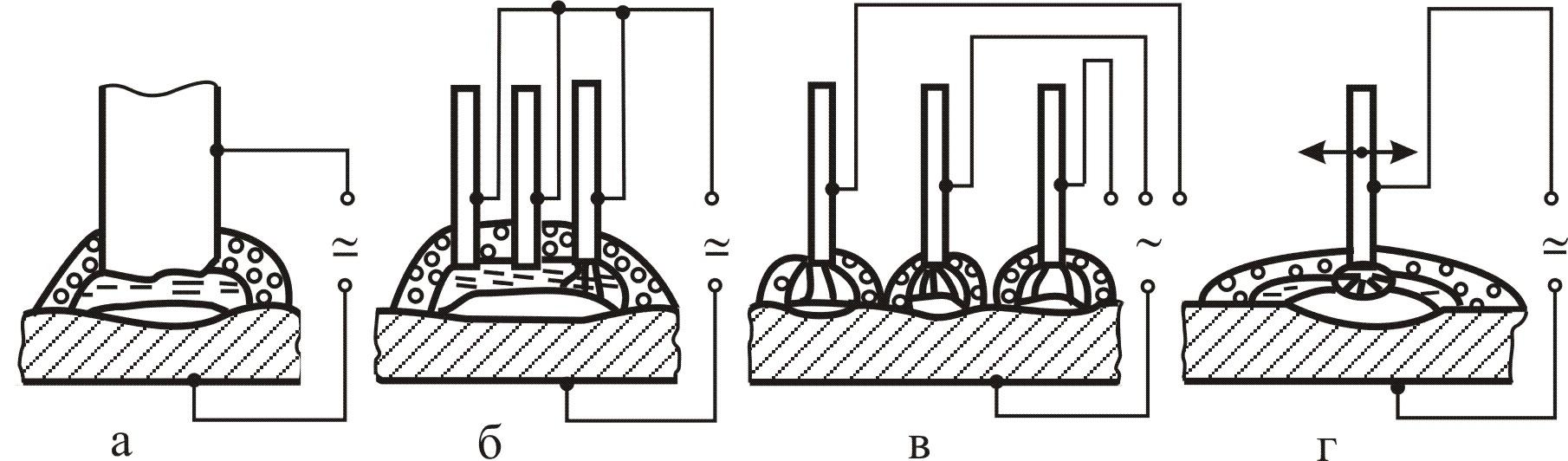
Рис.8.2. Способы наплавки под флюсом: а – электродной лентой; б – многоэлектродная; в – многодуговая; г – поперечным колебанием электрода
При многоэлектродной наплавке вследствие перемещения дуги с одного электрода на другой длительность ее горения на одном из электродов значительно меньше, чем при одноэлектродной. Это уменьшает длительность воздействия дуги на расплавленный металл ванны в определенном ее месте. В результате уменьшаются глубина кратера и проплавление основного металла.
Вибродуговая наплавка под флюсом. Стремление сохранить хорошие качества наплавки, получаемой под слоем флюса, и уменьшения остаточных деформаций привело к использованию вибрации электрода при наплавке, что обеспечивает надежное зажигание и горение дуги при весьма низких параметрах режимов. В сочетании с охлаждением наплавляемой детали данный способ дает существенное снижение остаточных деформаций при высоких механических свойствах.
Схема устройства для наплавки валов небольшого диаметра таким способом показана на рис. 8.3. Флюсоудерживающее приспособление 2 крепится к сварочной головке и перемещается вместе с ней. Для лучшего отделения шлака и охлаждения наплавляемой детали устанавливают охладитель 3, подающий сжатый воздух.
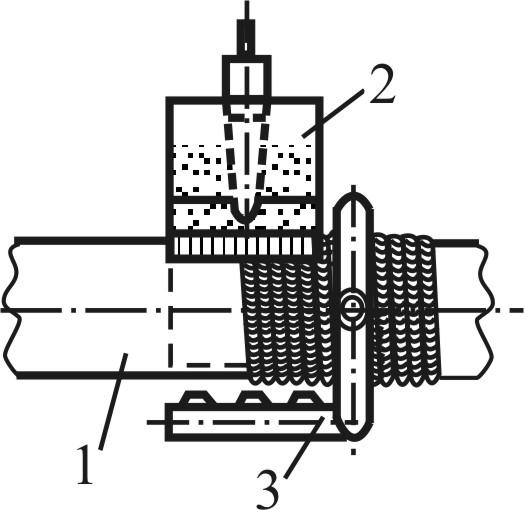
Рис.8.3. Схема вибродуговой наплавки под флюсом
Основные преимущества наплавки под флюсом: универсальность; высокая производительность; возможность получения наплавленного металла практически любой системы легирования; малые потери электродного металла; отсутствие излучения дуги.
Основные недостатоки: большое проплавление основного металла, особенно при наплавке проволоками; невозможность визуального наблюдения за формированием валиков; необходимость использования различных флюсоудерживающих и формирующих устройств; невозможность выполнения наплавки в пространственных положениях, отличных от нижнего; затрудненность удаления шлаковой корки при наплавке деталей малого диаметра и глубоких внутренних поверхностей.
Наплавка в среде защитных газов. Среди способов наплавки в среде активных защитных газов наибольшее распространение получила наплавка плавящимся электродом в среде дешевого и недефицитного углекислого газа. Этот способ позволяет наносить на детали небольших диаметров слои толщиной 0,5 – 3,5 мм высокого качества при высокой производительности. К недостаткам следует отнести повышенное разбрызгивание металла (до 15 %), необходимость применения специальной легированной проволоки для получения слоев высокого качества.
Перспективна наплавка в среде различных газовых смесей (12 % СО2 и 88 % Ar; 3 % О2 и 97 % Ar и др.). Этот способ дает возможность получать слои с высокими механическими свойствами, особенно по сопротивлению усталости и ударной вязкости.
Наплавку в среде инертного газа осуществляют неплавящимся и плавящимся электродами.
Для наплавки неплавящимся электродом в качестве неплавящихся электродов используются угольные (графитовые) стержни диаметром 5 – 40 мм и вольфрамовые прутки. При этом присадочный металл вводят в зону дуги в виде проволоки (прутка) или в виде порошка. При наплавке угольным (графитовым) электродом наплавочные порошки насыпают на наплавляемую поверхность, а затем расплавляют (см. рис.8.1, а). Наплавленный металл отличается невысоким качеством вследствие окисления легирующих элементов, образования пор, неметаллических включений и других дефектов. Наплавка вольфрамовым электродом в среде инертного газа характеризуется тем, что дуга, за счет теплоты которой происходит плавление наплавочного присадочного металла, возникает между основным металлом и вольфрамовым электродом (см. рис. 8.1, в). Процесс аргонодуговой наплавки, сходный с газовой наплавкой, протекает в условиях подачи наплавочного прутка и его плавления дугой.
Применение механизированных средств подачи наплавочного материала с постоянной скоростью позволяет осуществлять наплавку в автоматическом или полуавтоматическом режиме. Инертный газ хорошо защищает зону наплавки от воздушной атмосферы, поэтому данный способ особенно эффективен при наплавке цветных металлов, высоколегированных сталей и других материалов, чувствительных к окислению и азотированию. При этом используется широкая гамма наплавочных материалов и формируется наплавленный металл высокого качества. Стабильная дуга колоколообразной формы образуется в широком диапазоне силы тока, что обусловливает получение ровного валика наплавленного металла с гладкой поверхностью. Этот способ уступает наплавке плавящимся электродом по производительности из-за высокой концентрации энергии и низкой эффективности использования теплоты дуги.
Наплавка плавящимся электродом в среде защитного газа (см. рис. 8.1, г) характеризуется тем, что дуга возникает между основным металлом и электродным наплавочным материалом. Наплавка протекает в условиях автоматической подачи электродной проволоки. В качестве защитного газа чаще всего используют аргон, хотя при работе в среде чистого аргона дуга теряет стабильность при наплавке любого материала, кроме алюминиевых сплавов. С целью стабилизации дуги при наплавке стали к аргону добавляют до 20 % кислорода или углекислого газа, что существенно влияет на процесс наплавки. Поэтому задача получения наплавленного металла с заданными свойствами требует тщательного выбора состава защитного газа.
Дуговая наплавка самозащитными порошковыми проволоками и лентами в настоящее время получила большое распространение. Стабилизация дуги, легирование и защита расплавленного металла от азота и кислорода воздуха обеспечивается за счет соответствующих компонентов сердечника электродного материала. При этом газо- и шлакообразующие компоненты составляют 10 – 12 % массы проволоки или ленты (рис.8.4). Такая наплавка перспективна при упрочнении деталей сложной формы, когда наплавка их под слоем флюса затруднительна.
При плавлении такой проволоки легирующие элементы шихты и металла оболочки переходят в шов, образуя наплавленный металл. Наплавленный валик покрывается тонким слоем шлака, достаточным для защиты от воздействия воздуха и не требующим удаления при многослойной наплавке. Порошковые проволоки с внутренней защитой для автоматической и механизированной наплавки изготовляют диаметрами: 1,6; 2,0; 2,5; 2,8; 3,0; 3,2 мм.
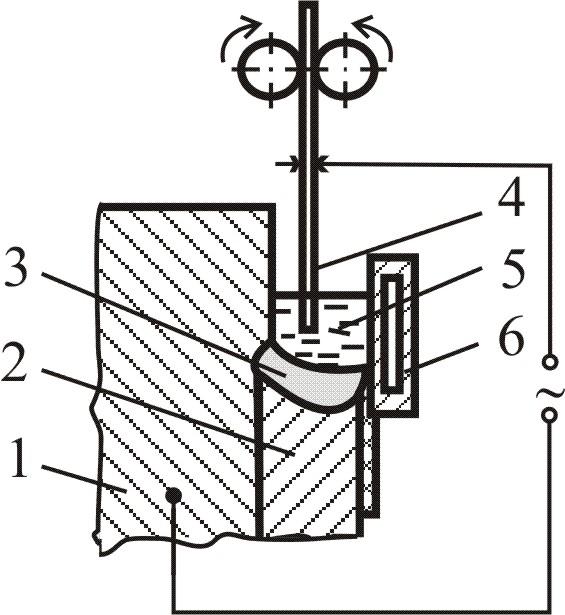
Рис. 8.4. Конструкции порошковых проволоки Рис.8.5. Схема электрошлаковой наплавки
(а) и ленты (б)
При наплавке крупных деталей вместо порошковой проволоки используется близкая по составу порошковая лента, что дает дополнительный выигрыш в производительности.