28.03.2023
Группа 510
Предмет: Эксплуатация и Т.О. С/Х машин и оборудования
Тема урока: Перевозка грузов
Цель урока: изучить данную тему, составить конспект урока
Особенности организации перевозок сельскохозяйственных грузов
К сельскохозяйственным грузам относятся: различная продукция сельскохозяйственного производства (зерно, овощи, фрукты, хлопок, продукты животноводства, растениеводства и др.), а также удобрения, посевные и посадочные материалы, топливо для сельскохозяйственных машин и различные хозяйственные грузы колхозов, совхозов и фермеров.
Сельскохозяйственные грузы классифицируются по следующим признакам: физико-механическим и биохимическим свойствам; степени использования грузоподъемности транспортных средств; способу погрузки- разгрузки; срочности и периодичности перевозок; массовости перевозок и условиям перевозок.
По физико-механическим свойствам различают грузы: твердые, жидкие или наливные (молоко, аммиачная вода, жидкое топливо и другие), газообразные.
К физико-механическим свойствам сельскохозяйственных грузов относятся также углы естественного откоса, коэффициенты трения, бокового давления и другие, которые влияют на конструкцию кузова и крепление его к раме. Около 70 % сельскохозяйственных грузов относится к насыпным и навалочным.
По срочности и периодичности перевозок различают грузы, подлежащие перевозке в сжатые сроки, лимитируемые агротехническими требованиями, либо скоропортящиеся, и грузы, перевозки которых могут быть растянуты на более длительный срок.
Основные виды сельскохозяйственных грузов (зерно, сахарная свекла, овощи, силос, комбикорм, сено прессованное) относятся ко второму классу.
По условиям перевозки грузы делятся на обычные - не требующие специализированного подвижного состава; скоропортящиеся - требующие соблюдения особых санитарных и температурных режимов; с резкими неприятным запахом - перевозимые в специально приспособленных кузовах; антисанитарные; живность.
В Нечерноземной зоне на каждый гектар посева зерновых приходится перевозить около 25 т различных грузов: 10-20 т органических удобрений, 0,5-1,0 т семян и минеральных удобрений, 2-3 т зерна, 3-4 т соломы, 2-3 т технических грузов.
При возделывании картофеля, свеклы и овощей на каждый гектар приходится перевозить органических удобрений 30-40 т, продуктов урожая 20-40 т, семян и минеральных удобрений 1-3 т.
Примерная структура объема перевозок сельскохозяйственных грузов, %:
Зерно ………………9,5
Картофель ………………7,3
Овощи ………………1,2
Сахарная свекла ………………4,2
Молоко ………………4,3
Корма (стойловый период) ...............34,5
Удобрение ………………35,0
Прочие продукты полеводства ……4,0
Итого: 100,0
К особенностям организации перевозок сельскохозяйственных грузов относятся:
резкие сезонные колебания объема работ и большие колебания потребности в подвижном составе по различным периодам года;
различные дорожные условия и расстояния перемещения грузов; привлечение на период уборки урожая подвижного состава и обслуживающего персонала различных организаций и ведомств;
срочность перевозок на период уборки урожая, при наличии мелких разбросанных на большой территории погрузочных, грузообразующих пунктов, при относительно небольшом числе приемных, грузопоглощающих пунктов;
необходимость создания на период уборки урожая временных заправочных пунктов, пунктов технического обслуживания и ремонта подвижного состава, питания и отдыха водителей;
осуществление транспортного обслуживания сельскохозяйственного производства собственными силами фермеров, колхозов и совхозов, автотранспортными предприятиями, находящимися в ведении агропромышленного комплекса, и автотранспортом общего пользования;
организация надежной диспетчерской связи между всеми пунктами, организациями и подвижным составом, занятым перевозками урожая.
Основным видом транспорта в сельском хозяйстве является автомобильный. На его долю приходится до 80 % объема перевозок грузов. Тракторным парком выполняется около 16 % объема перевозок грузов.
Перевозка и внесение удобрений. Применяемые в настоящее время удобрения делятся на органические и минеральные, на твердые и жидкие. К числу твердых, простых, минеральных удобрений относятся суперфосфат, фосфатная мука, хлористый и сернокислый калий, аммиачная селитра, сульфат аммония, мочевина. К сложным минеральным удобрения относятся нитрофоска и аммофос. К жидким удобрениям - жидкий аммиак, аммиакаты, аммиачная вода. К органическим удобрениям относятся навоз, фекалии, торф, компосты.
Перевозка и внесение твердых органических удобрений может осуществляться двумя способами. Первый способ - бесперевалочный (ферма-поле), второй - перевалочный (ферма-бурт-поле). При бесперевалочном способе навоз накапливают в навозохранилищах большой емкости или в штабелях, формируемых в непосредственной близости от животноводческих ферм, а затем вывозят на поле и разбрасывают. Перевозка и разбрасывание удобрений производится навозоразбрасывателями.
Когда расстояние от ферм до поля значительное, то удобрения доставляются к разбрасывателям автомобилями-самосвалами и тракторными поездами. В этом случае так называемая перегрузочная технология включает погрузку навоза в автомобиль-самосвал, транспортирование удобрений до поля, загрузку разбрасывателя (РПН-4) непосредственно из автомобилей-самосвалов, внесение удобрений разбрасывателем РПН-4.
При перевалочном способе удобрение вывозится из навозохранилища в поле и укладывается в штабель. В период внесения навоз загружается из штабеля в навозоразбрасыватели, которые вносят удобрение в почву.
Перевозка и внесение минеральных удобрений выполняются по следующей схеме. На заводе-изготовителе удобрения загружаются в железнодорожные вагоны, перевозятся до станции назначения и перегружаются в прирельсовые склады. Затем автомобильным транспортом удобрения доставляются в хозяйства и складируются в глубинных складах. При наступлении агротехнических сроков удобрения из этих складов перевозятся на поле и вносятся в почву.
В ряде случаев более выгодными являются прямые автомобильные перевозки удобрений с заводов-поставщиков колхозам, совхозам и фермерским хозяйствам. В результате сокращается объем погрузочно-разгрузочных работ, снижаются потери удобрений, ускоряются перевозки, высвобождаются людские ресурсы и железнодорожные вагоны, отпадает необходимость строительства прирельсовых складов. Результаты расчетов показывают, что прямые автомобильные перевозки экономичнее смешанных автомобильно-железнодорожных при расстояниях перевозки для автомобилей ЗИЛ-130 до 210 км, МАЗ-500 - до 290 км, MA3-504A+MA3-5345 - до 405 км, для МАЗ-504А с двумя прицепами МАЗ-5245 - до 700 км.
Внесение минеральных удобрений в почву выполняется тремя способами - прямоточным, перегрузочным и перевалочным.
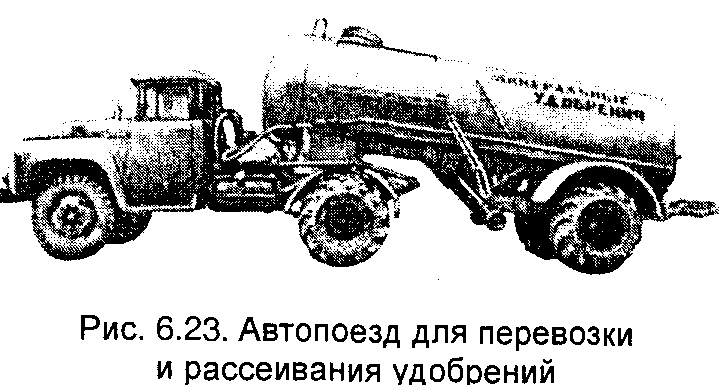
| При перевозке твердых минеральных удобрений навалом на участках прирельсовый склад - поле или завод - поле можно использовать автомобили- цементовозы большой грузоподъемности (рис. 6.23), у которых разгрузочный шланг заменен гофрированым рукавом, соединенным с трехрожковым распылителем. |
Внесение удобрений в почву происходит при движении автомобиля - цементовоза по полю.
Себестоимость распыливания удобрений в этом случае примерно в 4 раза ниже, чем при использовании специальной сельскохозяйственной машины-рассеиватля.
Жидкие минеральные удобрения вносят как при основной и предпосевной обработках почвы, так и в период ухода за посевами сельскохозяйственных культур.
Широкое применение имеет водный аммиак. Водный аммиак с заводов в районы его применения перевозят в специальных железнодорожных цистернах. Из цистерн удобрения перекачиваются в пристанционные хранилища, откуда их перевозят в автомобилях-цистернах на склады сельскохозяйственных предприятий. Со складов автомобилями- цистернами или тракторными заправщиками жидких удобрений они перевозятся в поле. Внесение удобрений в почву производится универсальными подкормщиками-опрыскивателями, которые работают в комплексе с плугами или культиваторами. В ближайшие годы технология внесения жидкого аммиака будет выполняться по прямоточной схеме «завод- поле», которая предусматривает хранение аммиака при заводе и поставку его автомобильным транспортом в период применения. Прямые автомобильные перевозки целесообразны при расстоянии от завода до поля до 60 км.
Перевозка зерна. Затраты на транспортирование зерна составляют 25-30 % от общих затрат на его производство. Поэтому снижение трудовых и материальных затрат на перевозку зерна - важнейший источник снижения себестоимости и трудоемкости его производства.
Во время уборки урожая автомобили перевозят зерно по следующим технологическим схемам:
комбайн - зерноочистительно-сушильный ток - элеватор; комбайн - элеватор;
комбайн - зерноочистительно-сушильный ток - склад - элеватор. Прямые перевозки зерна с полей к местам первичной его обработки осуществляются по схеме комбайн - ток.
Основное требование, предъявляемое к построению поточных процессов уборки урожая, заключается в обеспечении работы комбайнов (базовых машин) без простоев из-за отсутствия транспортных средств. До недавнего времени применялось индивидуальное закрепление автомобилей за комбайнами. За каждым комбайном закреплялось 1-2 автомобиля. При такой системе автомобили простаивали в ожидании загрузки из-за разности объемов бункера комбайна и кузова автомобиля, а комбайны простаивали из-за неравномерности прибытия автомобилей под погрузку.
В настоящее время уборка зерна осуществляется комплексными убо- рочно-транспортными бригадами, состоящими из комбайнеров и водителей. Различают мелкогрупповую работу (2-4 комбайна), среднегруп- повую (5-10 комбайнов) и крупногрупповую работу (свыше 10 комбайнов). Опыт показывает, что наиболее рациональный размер бригады, когда она имеет в наличии 8-10 комбайнов. При этом:
уменьшаются простои автомобилей в ожидании погрузки по сравнению с индивидуальным их закреплением; возрастает выработка комбайнов;
создаются возможности более эффективной организации технического обслуживания и текущего ремонта комбайнов.
Увеличение числа комбайнов в бригаде усложняет управление бригадой и учет качества работы отдельных комбайнеров.
К особенностям работы автомобилей, обслуживающих зерноуборочные комбайны, относятся:
значительное различие в режимах движения автомобиля по дороге и полю;
выполнение сборочных операций при постоянном перемещении объекта обслуживания;
влияние на степень готовности комбайна к разгрузке значительного количества факторов - колебаний урожайности по площади поля, простоев из-за неисправности и других, вследствие чего их процесс взаимодействия с автомобилями носит вероятностный характер.
Время пребывания автомобиля на поле, даже при уборочно- транспортных комплексах, достигает 62-78 %. Баланс сборочно- транспортного процесса складывается из:. ожидания погрузки - 40-68 %; времени переездов по полю - 19-40 %; времени на погрузку - 13-20 %.
Для улучшения взаимодействия транспортных средств и комбайнов на поле прокладывают разгрузочные и транспортные магистрали. Разгрузочные магистрали представляют собой поперечный прокос поля шириной 6-8 м. Они прокладываются с таким расчетом, чтобы между ними комбайн намолачивал целый бункер зерна и разгружался на магистрали.
Разгрузочные магистрали позволяют автомобилям двигаться к местам погрузки по одному и тому же маршруту, в результате чего на поле появляется накатанная дорога, что дает возможность повысить техническую скорость до 20 км/ч и использовать автопоезда.
Бортовые автопоезда (рис. 6.24) находят широкое применение на перевозках зерна с токов на хлебоприемные пункты, что сокращает потребность в подвижном составе, и снижает себестоимость перевозок.
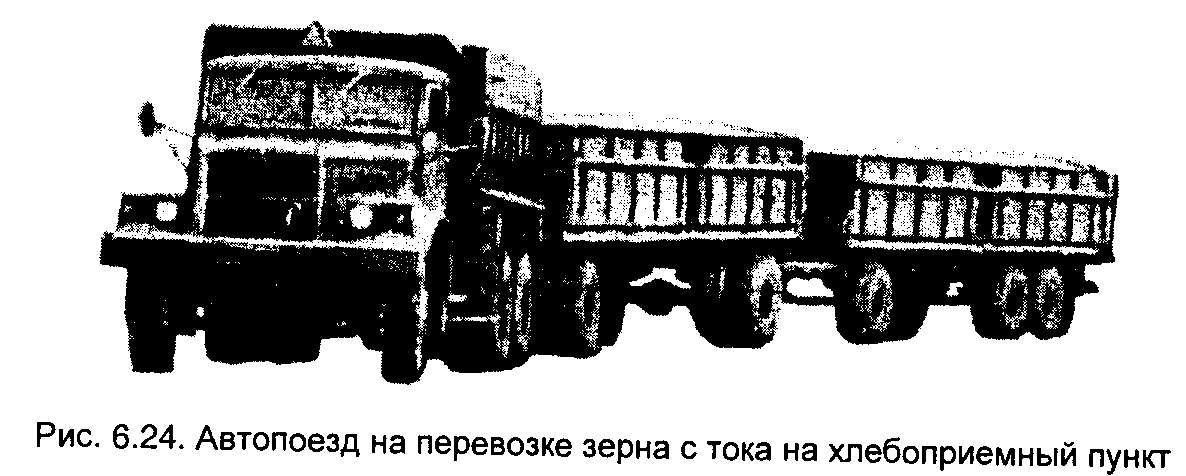
Для определения технологически необходимого времени простоя автомобилей в ожидании погрузки применяется математический аппарат теории массового обслуживания. В математической модели уборочно-транспортная бригада представляется в виде системы массового обслуживания с ожиданием, в которой обслуживающим аппаратом является автомобиль, обслуживаемым - комбайн. Система массового обслуживания замкнутая, с ограниченным числом автомобилей.
Поступившее в систему требование (остановка комбайна с полным бункером), застав все автомобили занятыми загрузкой других комбайнов, вынуждено ожидать своей очереди до тех пор, пока не освободится один из автомобилей. После обслуживания (разгрузки бункера) комбайны через некоторое время вновь становятся на обслуживание и т. д. Вероятностный характер уборочно-транспортного процесса предопределяет взаимообусловленные простои комбайнов и автомобилей. Для устранения простоев в технологическую цепочку вводится промежуточное звено - компенсатор, и перевозки осуществляются по схеме комбайн - компенсатор - автомобиль - ток.
В зависимости от выполняемых функций компенсаторы делятся на межоперационные и межсменные. Первые дают возможность организовать «независимую» работу комбайнов и автомобилей, на протяжении времени работы комбайнов, вторые - использовать автомобили в две-три смены при односменной работе комбайнов.
По характеру работы компенсаторы делятся на передвижные, стационарно-передвижные и стационарные. Роль компенсаторов могут выполнять автомобильные и тракторные прицепы, полуприцепы, различного рода бункера и т. п.
Недостатки при применении компенсаторов: отсутствие заранее установленных мест разгрузки комбайнов; необходимость в некоторых случаях подъезда комбайна к компенсаторам; значительное увеличение потребности в прицепном составе или необходимость строительства на каждом поле стационарных компенсаторов; ограниченность объема стационарных компенсаторов и др.
Перевозка сена, соломы и силосной массы. Сено и солому перевозят из стогов и скирд в обычном или в прессованном виде. В первом случае их перевозят навалом, во втором как штучный груз. Для механизации погрузки сена навалом используют стогометатели, применяемые также при скирдовании.
Перевозка силосной массы по количеству занимает особое место в сельскохозяйственных перевозках, особенно если учесть небольшую ее плотность. Грузоподъемность подвижного состава используется лишь на 40-45 %, поэтому борта кузова должны быть увеличены по высоте (рис. 6.25). В связи с небольшим расстоянием перевозок (на 1-3 км) целесообразно применять тракторные прицепы или автомобили-самосвалы также с увеличенным объемом кузова.
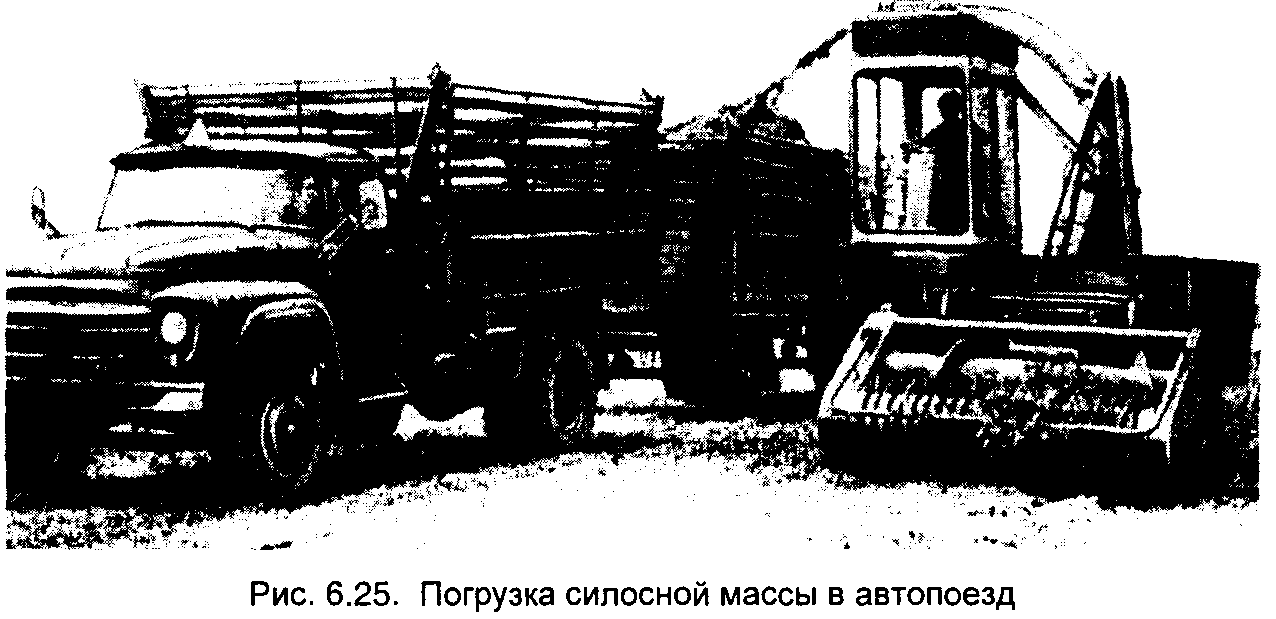
Перевозки живности и продуктов животноводства и птицеводства. Перевозка животных вызывает изменение привычного режима их содержания, связанное с новыми условиями размещения, тряской в пути, погрузкой и разгрузкой. Все это приводит животных к нервному возбуждению, отказу от корма, отрицательно сказывается на массе животных.
Автомобильный транспорт при массовых перевозках животных на приемные пункты, а также на мясокомбинаты и бойни целесообразно использовать при расстоянии перевозки до 500 км. Живность следует перевозить с учетом климатических особенностей местности.
Специализированный подвижной состав для перевозки животных должен удовлетворять следующим требованиям:
создавать условия, обеспечивающие минимальные потери в живой массе и предотвращающие повреждения животных во время перевозки;
обеспечивать удобную погрузку и выгрузку животных при минимальных простоях под этими операциями;
давать возможность использовать эти автомобили для перевозок другого груза в межсезонный период.
Наиболее целесообразно для этих целей использовать автомобили- тягачи с полуприцепами-фургонами (рис. 6.26). Кузов полуприцепа фургона должен иметь прямоугольную форму длиной не менее 8,5 м, обеспечивать естественную приточную вентиляцию в верхней и нижней частях, иметь ровную поверхность пола, боковую дверь и дверь-трап в задней части, внутреннее электрическое освещение и жижесборники. Для деления на отсеки внутри кузов должен быть оборудован съемными перегородками с кольцами для привязи животных. Полуприцепы фургоны имеют вместимость 16 голов крупного рогатого скота или 55 свиней. Модель полуприцепа в двухъярусном варианте позволяет разместить 140-175 овец.

При использовании бортовых автомобилей для перевозки животных необходимо нарастить борта до 1,5-2 м и разделить кузов на 2-3 отсека для предупреждения скучивания телят, овец, свиней на подъемах и спусках. Крупные рогатые животные должны быть привязаны головами вперед по ходу движения.
Специализированный подвижной состав используется и на перевозках птицы. Взрослую птицу перевозят в многоярусных контейнерах, помещаемых на платформу специальной конструкции. Молодняк птицы перевозят в специальных ящиках, которые устанавливают в изотермические кузова автофургонов, обеспечивающих микроклимат. Вместимость автофургона - 6000 цыплят или утят, 8000 индюшат.
Широкое распространение имеют перевозки однодневных цыплят и инкубационных яиц на достаточно большие расстояния с межхозяйственных, инкубаторно-птицеводческих станций в колхозы и совхозы. Внутри кузова размещаются контейнеры, в которые ставятся ящики с цыплятами или яйцами. Вместимость - около 29,2 тыс. яиц или 14,4 тыс. однодневных цыплят.
На отправляемую живность грузоотправитель обязан предоставить свидетельство, выданное ветеринарным органом. Это свидетельство, без которого перевозка не разрешается, должно быть составлено на каждую партию живности (на каждый автомобиль или несколько автомобилей при одновременной их отправке одним грузоотправителем в адрес одного грузополучателя).
Перед отправкой из хозяйства крупный рогатый скот и лошади должны быть забиркованы, свиньи - забиркованы или татуированны, овцы - мечены. Затем живность взвешивают, формируют партии - гурты и выписывают гуртовую ведомость, где особенно отмечают наличие травм и повреждений кожного покрова у животных.
Гуртовые ведомости заполняют: на крупный рогатый скот - на основании взвешивания каждой головы с указанием номера, пола, возраста, упитанности и массы; на свиней, овец, коз и кроликов - по группам животных с одинаковой упитанностью; на птицу - по видам и возрасным группам.
При автомобильный перевозках скота даже при соблюдении всех правил происходит уменьшение их массы. Причем эти потери тем больше, чем длительнее перевозка, и достигают 5 % при расстояниях более 100 км.
При дальних перевозках животных должен сопровождать проводник - экспедитор. На постоянных и массовых перевозках обязанности экспедитора могут быть возложены на водителя.
Молоко в сельском хозяйстве можно перевозить в неохлажденном или охлажденном виде. Свежевыдоенное молоко - благоприятная среда для быстрого размножения микроорганизмов, приводящих к скисанию молока. Поэтому с пунктов, не имеющих условий для немедленного охлаждения и хранения молока (пастбищ, небольших ферм, у населения), вывоз должен производиться сразу же после каждой дойки. Однако и там, где имеются установки для охлаждения и хранения, молоко при температуре не выше плюс 10 °С должно храниться не более 20 ч.

| Молоко является скоропортящимся продуктом и организация его перевозок должна обеспечивать четкий, бесперебойный и своевременный вывоз его с пунктов производства в пункты переработки (молокозаводы). Молоко можно перевозить в специализированных цистернах на шасси автомобилей (рис. 6.27), полуприцепов и двухосных прицепов при бестарной перевозке или на бортовых автомобилях при перевозке в металлических флягах вместимостью до 40 л. |
Вместимость цистерн - от 1900 до 22000 л. Термоизоляция обеспечивает изменение температуры молока не более чем на 2-3 °С при температуре окружающего воздуха ±30 °С в течение 10 ч.
Цистерны и фляги должны быть поданы под перевозку чистыми и продезинфицированными или обработанными паром. При заливе они должны быть заполнены полностью, чтобы во время перевозки молоко не взбалтывалось. Затем плотно закрыты крышками с прокладками из пищевой резины и опломбированы.
Особой формой перевозок молока является сбор молока у населения (индивидуальных молокосдатчиков). Для этого разрабатывают кольцевой сборный маршрут и график движения на нем. Молоко во флягах размещается сдатчиками на сборных пунктах (помостах высотой 1,0-1,1 м с трехступенчатым трапом), места, размещения которых расположены вдоль дороги.
На водителя кроме сбора молока и слива его в цистерну возлагают обязанности регистрации количества сдаваемого молока и снятия проб (по каждому молокосдатчику) с помощью специального оборудования, выдаваемого ему молокоперерабатывающим предприятием.