21.09.2022
Группа 401
Предмет: Технология механизированных работ в С/Х
Тема урока: Устройство зерновой сеялки
Цель урока: изучить данную тему, составить конспект урока.
Для сева колосовых на зерно используют в большей степени зерновые сеялки СЗ-3,6А, СЗ-5,4, СЗ-10,8 и их модификации.
Зернотуковая сеялка СЗ-3,6А (рис.5) состоит из двух ящиков 1, двух секций высевающих аппаратов 17, закрепленных внизу к днищу каждого ящика, двух секций туковысевающих аппаратов 2, установленных в задней стенке тукового отделения ящика, резиновых гофрированных семяпроводов 11, дисковых сошников 7, 12, загортачей 8, двух опорно-приводных колес 3, зубчато-цепного механизма привода высевающих аппаратов 4, механизма подъема сошников, гидроцилиндра 16 и прицепного устройства 15. В ящике установлена перегородка, которая делит ящик на два отделения: переднее – для семян и заднее – для удобрений. В перегородке есть окна, которые открываются и при необходимости оба отделения ящика можно использовать для засыпки семян. Сверху ящики закрываются двумя крышками.
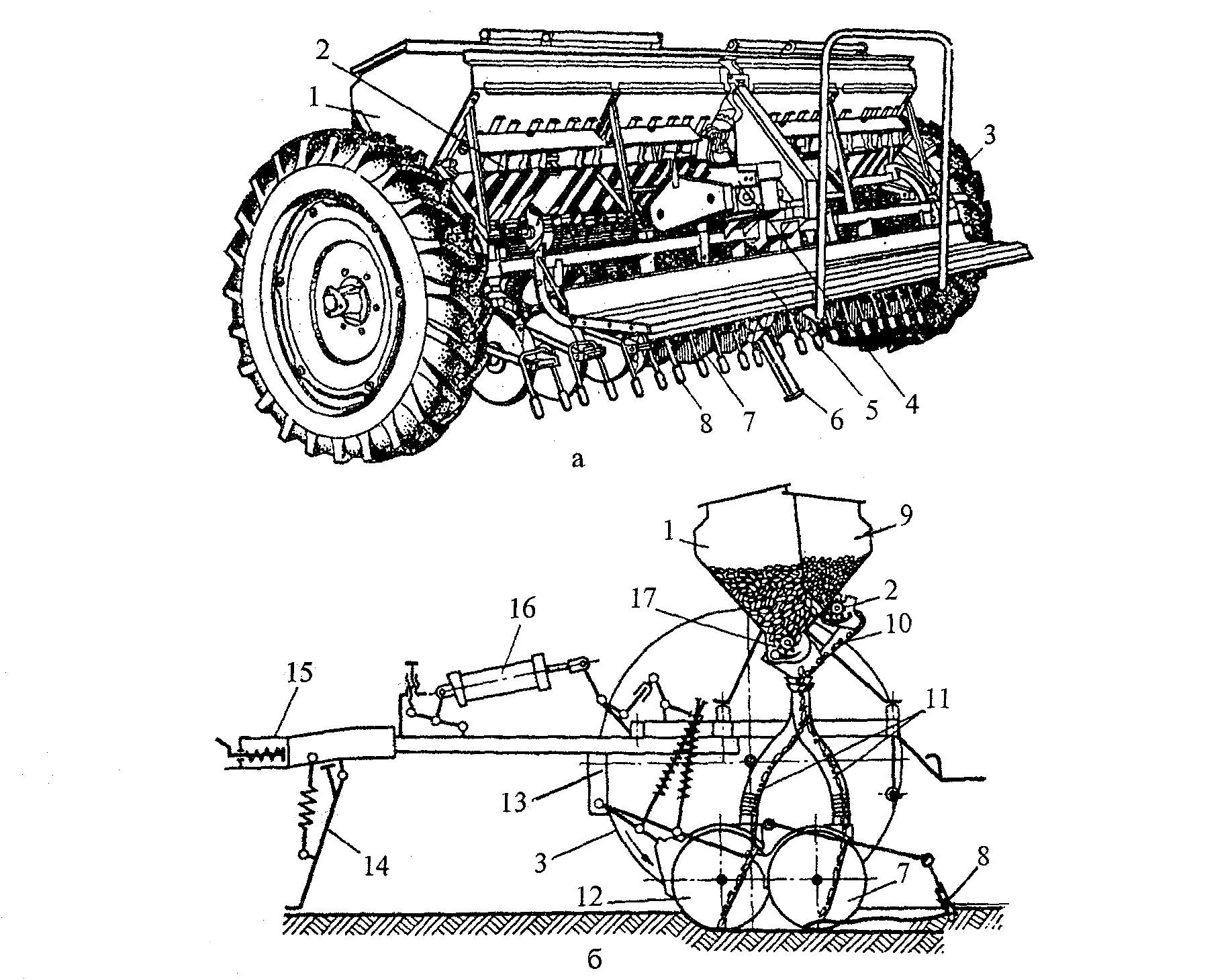
Рис. 5. Зернотуковая сеялка СЗ-3,6А
а- общий вид; б- функциональная схема; 1- зернотуковый ящик; 2- высевной аппарат для туков; 3- опорно-приводное колесо; 4- коробка передач; 5 - подножная доска; 6 и 14- подставки; 7- сошник задний; 8- загортач; 9- отделение ящика для удобрений; 10- лоток; 11- семяпроводы; 12- передний сошник; 13- рама; 15- прицепное устройство; 16- гидроцилиндр; 17- семявысевающий аппарат
и семян. Каждый ящик закрывается
Рабочий процесс. Во время работы сеялки от опорно-приводных колес 3 приводятся во вращение катушки для высева семян 17 и удобрений 2. Они захватывают семена и удобрения и подают их в семяпроводы 11. После этого семена и удобрения попадают в сошники 7 и 12 и ложатся на дно борозды. Загортачи 8 засыпают семена и удобрения на дне борозды. Рабочая ширина захвата сеялки 3,6м. Глубина хода сошников 4-8см. Емкость зернового отделения ящика 453 дм3, а тукового 212 дм3. Рабочая скорость до 12 км/час. Производительность 3,6 га/час.
Рабочими органами зерновых сеялок являются высевающие аппараты, сошники и загортачи.
Высевающие аппараты – это дозаторы, которые отбирают часть семян из ящика сеялки и направляют их в сошники. Их задача –создать равномерный и беспрерывный поток семян или удобрений, обеспечить устойчивость их высева в независимости от скорости движения посевного агрегата и рельефа почвы. По принципу действия дозаторы зерновых сеялок могут быть механическими, пневматическими и электромагнитными.
Механические высевающие аппараты подразделяются на катушечные, катушечно-штифтовые и вибрационные. Основные из них – катушечного типа. Они являются универсальными дозаторами при высеве зерновых культур. На современных сеялках катушечные аппараты устанавливают с нижним высевом, а для крупносемянных культур (горох, фасоль, бобы) – с верхним высевом для уменьшения степени механического травмирования семян.
К основным частям катушечного высевающего аппарата (рис.6) относятся: семенная коробка, катушка 1, муфта 9, вал 4 и подпружиненный клапан 6.

Рис. 6. Высевающие аппараты катушечного типа
а, б- рядовых сеялок; в- травяных сеялок; г, д- овощных сеялок. 10 и 24- катушки; 2- розетка;19 - корпус; 4, 11 и 15-валы; 5- ребро муфты; 6, 12, 16- клапаны; 7- регулировочный болт; 8- ось; 9- муфта; 13- заслонка; 14- неподвижное дно; 17 и 22- пружины; 18- ворошилка; 20- диск; 21- окно; 23- болт
Семенная коробка крепится к днищу зернотукового ящика. Катушка закреплена на валу 4 и вращается при работе вместе с валом. В нижней части коробки на оси установлен вогнутый в середину криволинейный клапан 6 для опорожнения семенного ящика.
Рабочий процесс. Семена из зернового ящика высыпаются в корпус 3 высевающего аппарата. Во время вращения катушки семена заполняют ее желобки и перемещаются к семяпроводам. Количество высевающих семян зависит от длины рабочей части катушки и скорости ее вращения, которая регулируется с помощью смены передаточного отношения зубчатой и цепной передачи. Это достигается перемещением шестерен в редукторе или сменой звездочек в цепной передаче. Длину рабочей части катушки устанавливают рычагом регулятора высева путем перемещения его левее или правее вала с катушками. Катушки высевающих аппаратов сеялки должны иметь одинаковую рабочую длину. Ее проверяют при помощи шаблонов, а регулируют компенсационными шайбами на валу аппаратов и перемещением семенной коробки относительно дна ящика. Отклонение длины рабочей части катушки от заданной должно составлять + 1см. Катушки работают без повреждения семян при длине ее рабочей части не менее двух максимальных размеров семени. В зависимости от размера семени устанавливается зазор между клапаном и нижним ребром муфты высевающего аппарата: 0-2 мм для зерновых колосовых и 8-10 мм для крупносемянных бобовых культур.
Катушечно-штифтовые аппараты (рис.6б) также могут ставиться на зерновые сеялки. У них норма высева регулируется частотой вращения катушки и заслонкой 13. Для высева мелкосемянных культур на вал аппаратов устанавливают сменные катушки с зубчатой поверхностью, а для крупных семян в комплект входят катушки со специальными буртиками с ребрами.
На зерновых сеялках «Клен» устанавливается высевающая система с электроприводом и электронным приводом из кабины. Она состоит из дозатора, пульта управления, мультиплексора и датчика скорости движения. У дозатора имеется электропривод с микропроцессорным управлением.
На современных широкозахватных сеялках и комбинированных агрегатах устанавливают пневмомеханические высевающие аппараты с централизованным дозированием семян. Подачу семян из бункера обеспечивает дозатор катушечного типа, а транспортировка семян по пневмоприводам и семяпроводам осуществляется воздушным потоком.
Сошники являются вторым основным рабочим органом зерновых сеялок. Они служат для создания в почве бороздки и укладки на ее дно семян и удобрений. От качества работы сошников в значительной мере зависит появление равномерных дружных всходов и развитие растений. Сошники должны создавать одинаковые борозды заданной глубины, не выносить нижние слои почвы на поверхность поля, чтобы не было потери влаги, уплотнять дно борозды для обновления капилляров в почве, обеспечивать равномерное распределение семян в борозде, присыпание их влажным слоем почвы. Наиболее распространенным типом сошников является двухдисковый однорядковый (обычный) сошник (рис.7) и килеподобный сошник (рис.8).
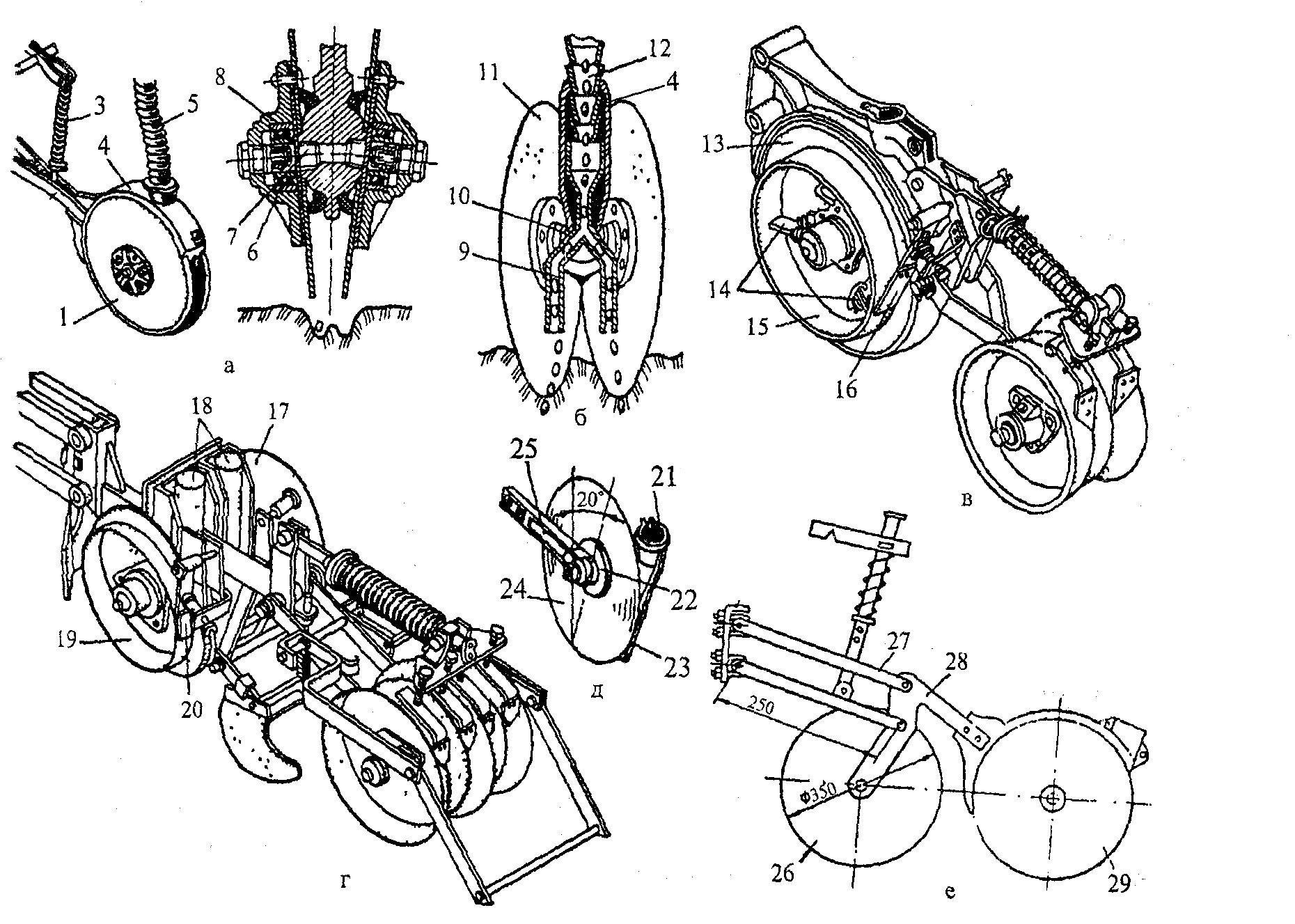
Рис.7.Дисковые сошники
а– двухдисковый однострочный; б–двухдисковый двухстрочный; в– двухдисковый однострочный с ребордами; г– двухдисковый двурядковый с ребордами; д– однодисковый; е– двухдисковый с дисковым ножом.; 1, 11, 13, 17, 24– диски; 2– поводок; 3– штанга с пружиной; 4– корпус сошника; 5 и 12– семяпроводы; 6–подшипник; 7 и 10 – оси дисков; 8- крышка; 9– распределитель; 14, 25 и 28 –кронштейны; 15 и 19 – реборды; 16, 20 и 23– чистики; 18 и 21- лейки; 22– ступица; 26– дисковый нож; 27– подвеска; 29– сошник дисковый.
Двухдисковый однорядковый (обычный) сошник состоит из двух плоских дисков 1, корпуса 4 с раструбом и поводком 2. К дискам прикрепляютсяфигурные крышки 8, в которые вставлены оси 7 с подшипниками 6. Кромка дисков разрезает почву и поэтому заостренная.
В передней части диски сходятся, образуя клины с углом 10º. Зазоры между ними должны быть не меньше 1,5 мм. В задней части корпуса сошника закреплены два чистика и направляющая пластина для направления семени на дно борозды. Между корпусом и дисками установлены резиновые уплотнители. При движении сошника диски 1 вращаются, разрезают почву и смещают ее на обе стороны, создавая борозду. Семена и минеральные удобрения по направляющей пластине попадают на дно борозды. Стенки борозды осыпаются и частично присыпают семена и удобрения почвой. Внутренние поверхности дисков очищаются чистиками.
Глубина хода дискового сошника регулируется винтом регулятора глубины сеялки, а устойчивость хода – сжиманием пружины штанги 3 сошника.
Килеподобный сошник (рис.8) имеет в передней части заостренную пластину (киль) 6, которая перемещает частички почвы сверху вниз и уплотняет дно борозды. Глубина хода сошника регулируется давлением пружины или тягой.

Рис.8. Сошники
а– анкерный; б– килеподобный сеялки СЗТ-3,6А; в– килеподобный сеялки СЗ-3,6А; г– килеподобный льняной сеялки; д– полозовидный комбинируемый; е и є– стерневых сеялок; ж– трубчатый; 1– киль; 2 и 15– кронштейны; 3– скоба; 4 и 23– трубки; 5, 8– лейки; 6- килеподобные лемеха; 7– полоз; 9- пятка; 10– болт; 11 и 17– пружины; 12 и 19–стойки; 13 и 20– лапы; 16– тяга; 18– семяпровод; 21 и 22– носок.
Сошники сеялок должны обеспечивать заделку минеральных удобрений на 2-3 см глубже семян и смещение вбок от рядка на 3-5 см.
Глубина хода сошников регулируется винтом регулятора глубины, а стойкость хода сошников обеспечивается сжатием пружин натяжных штанг.
Рабочие органы для загортания борозд (загортачи) являются третьим основным органом зерновой сеялки (рис. 9).

Рис.9. Рабочие органы для загортания борозд
а и б- пальцевые загортачи; в - шлейф кольцевой; г - шлейф цепной; д- боронка кольцевая; е- прикатывающий каток; є- каток с пальцевыми загортачами; ж- пальцевые загортачи с катком с- каток клиновидный; и- катки конические; л- дисковые загортачи; 1 и 10- зубы; 2- стояк; 3- скоба; 4- наральник; 5- сошник; 6, 8 и 9- кольца; 12- цепи; 11, 13, 16-обрезиненные катки; 14 и 15- полки; 17- клинообразные катки; 18, 19- катки конусообразные; 20- сферический диск; 21- полуось
Рабочие органы предназначены для полного загортания семян и борозд, выравнивания поверхности поля.
Пальцевые загортачи являются основными для зерновых сеялок. Они изготовлены в виде заостренных зубьев 1 на пружинных стойках 2 или в виде прутиков цилиндрического или овального сечения.
На сеялке СЗ-3,6А устанавливают пробоотборник семян, унифицированную систему контроля технологических параметров (УСК) и приспособление для перекрытия семявысевающих аппаратов.
Пробоотборник семян (рис. 10) установлен на зерновой сеялке СЗ – 3,6А под тремя правыми крайними высевающими аппаратами. Он состоит из лотка 1, крышки 2, трех леек 5 и пружины 3. Нижняя часть лотка прикреплена к семяпроводам. При взятии проб лоток 1 опускается и семена из лейки попадают на его дно. В рабочем положении сеялки крышка 2 поднята, и лейки 5 заходят в лоток. Семена из высевающих аппаратов попадают в лейки, а оттуда – в семяпроводы и сошники.

Рис. 10. Пробоотборник семян
1- лоток; 2- крышка; 3- пружина; 4- скоба; 5- лейка; 6 и 8- шплинт; 7- крючок; 9- трубка
Унифицированная система контроля призвана обеспечить групповой контроль за высевом семян и уровнем семян и удобрений в зернотуковом ящике. Она состоит из датчиков высева семян, датчика уровня семян и удобрений в ящиках, кабеля и пульта управления. Работает от напряжения 12В. При работе сеялки и подаче посевного материала к семяпроводам (семена проходят между фотоприемником и лампой) информационный сигнал на пульт не приходит. Если высев семян приостанавливается, то через полторы секунды на пульте включается звуковой сигнал, и на световом индикаторе загорается соответствующая лампочка. При снижении уровня посевного материала ниже места установки датчика в зернотуковом ящике появляется свободное пространство (незаполненное зерном или туками) между лампой и фоторезистером, и на пульте у тракториста загорается световой индикатор
(Уров. СУ) и подаются одиночные звуковые сигналы.